>Качество — прежде всего
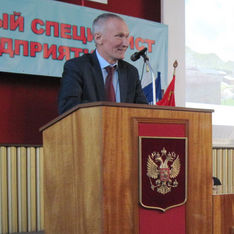
На протяжении всего времени с момента выпуска первого отремонтированного мотора и первой выпущенной машины у ОАО ААК «Прогресс» всегда был девиз: «Качество — прежде всего».
На днях на предприятии состоялось заседание Совета мастеров под председательством Владимира Григорьевича Бондаренко. На первый взгляд — рядовой эпизод из обычных будней заводчан. Однако этот день стал для коллектива предприятия еще одним шагом на пути к модернизации и усовершенствованию технических и технологических процессов в области качества.
В своих выступлениях перед коллективом на собраниях управляющий директор завода «Прогресс», председатель Приморского регионального отделения Союза машиностроителей России Юрий Петрович Денисенко всегда отмечает, что вопросы качества — это наиболее актуальные на сегодняшний день вопросы, которые необходимо решать.
«Качество должно закладываться на всех этапах жизненного цикла продукции: при проектировании, на этапе подготовки производства, при серийном производстве, при обеспечении эксплуатации, — говорит Юрий Петрович. — Для нас качество — это лицо предприятия, его честь и авторитет. Сегодня на предприятии многое уже сделано по обеспечению качества выпускаемой продукции. Есть положительная динамика, но нам также есть еще над чем работать.
Обеспечение качества на технологическом уровне — самый важный вопрос. Внедрение современных инновационных технологий — залог качества новой продукции. Организация планирования и культура производства — одни из составляющих качества».
Что же происходит на самом деле? На заседании были приведены неутешительные цифры. В 2014 году возросло количество дефектов на одну машину по сравнению с 2013 годом. Но здесь надо отметить, что возросло и количество предъявлений. Другими словами, количество предъявляемых деталей и узлов увеличилось в 1,4 раза. Дефекты действительно отслеживаются на конструкторских, технологических, производственных этапах. Эффективность технологических систем определяют три фактора: качество выпускаемой продукции, производительность и число рабочих, занятых в производстве. Суммируя все показатели, можно наблюдать уменьшение затрат на брак в 2014 году почти в 4 раза по сравнению с 2013 годом.
Если брать количество дефектов по каждому отдельному цеху, то среди них лидирует цех окончательной сборки, который несет наибольшую ответственность на этапе выпуска боевой машины. Здесь в совокупности затрагиваются все вопросы, в частности, и организации труда.
«Система внедрения бережливого производства, система 5С — слабое место на нашем предприятии. Мы медленно идем по пути внедрения этих технологий. Но это очень важный вопрос. Культура производства — это целая идеология сознательного подхода к своему делу. Организация труда, организация рабочих мест — это составляющие элементы качества.
Насколько мы сможем построить систему мониторинга и анализа качества поступающих к нам покупных комплектующих изделий, настолько мы обеспечим надежность и безотказность выпускаемой авиационной техники.
Организация входного контроля должна быть налажена со смежниками на уровне сервисных центров. С головным разработчиком ПКИ необходимо выстраивать взаимосогласованные программы по повышению качества изделий. Это то, над чем сегодня нам нужно серьезно работать», — отмечает директор предприятия.
Действительно, в цехах проведена большая работа по этапному внедрению бережливого производства. Наведен порядок на многих рабочих местах. Но до сих пор прослеживается отрицательная динамика в выявлении и анализе причин возникновения дефектов вследствие большого количества исполнительских и производственных причин в цехах основного производства.
Очень маленький и растущий в медленном темпе показатель количества человек, работающих на самоконтроле. В прошлом году всего 10 работников получили такое право. Сейчас на предприятии трудятся 110 человек, которые имеют клеймо качества и несут полную ответственность за свою продукцию, являясь положительным примером для всех работников авиакомпании. Это маленькая толика ответственных и грамотных специалистов в огромном коллективе авиастроителей. Так может, отринуть предрассудки и лень и держать равнение на лидеров? Не гонясь за количеством, стоит обратить внимание на качество выпускаемой продукции.
Совет мастеров совместно с мастерским составом предприятия проработал проблемы, стоящие перед цехами. На начальном этапе руководителям цехов рекомендовали при анализе причин возникновения несоответствий и классификации производственных и исполнительских дефектов аналитическими группами обязательно включать в их состав производственных мастеров. Помимо этого, цеховым комиссиям было рекомендовано при подведении ежемесячных итогов работы мастерских групп особое внимание уделять качеству выпускаемых изделий, выдвигать на материальное поощрение из «Фонда мастера» группу с хорошими показателями по качеству. А также всему руководящему составу цеха, включая работников БТК, было предложено развернуть работу по выявлению лучших производственных рабочих по качеству и доверию им личного клейма качества.
Не стоит забывать, что для рабочих мастер — первый руководитель. Мастер — это ключевое звено, ключевая фигура на заводе, на производстве, которая может реально влиять на ситуацию, менять ее к лучшему. Это то звено, которое связывает руководителей предприятия с рабочими. Необходимо максимально открыто и честно общаться с подчиненными, доводить до них максимум информации о происходящем и вовлекать сотрудников в процесс принятия решений. И ведущая роль в этом по-прежнему за мастерами, которые день за днем, шаг за шагом ведут вверенный им участок к общей цели — выполнению государственного заказа с отличным качеством.