>Эталонный участок по внедрению системы KANBAN
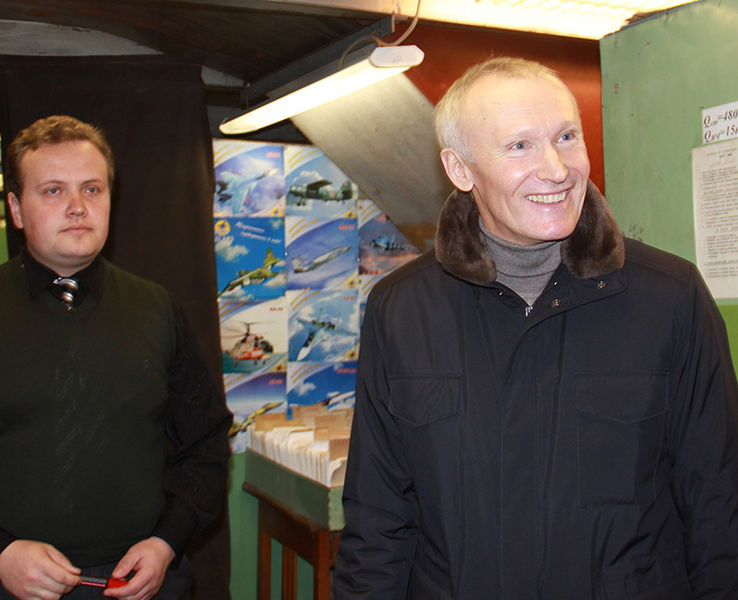
На днях управляющий директор ОАО ААК «Прогресс» Юрий Петрович Денисенко и заместитель директора по управлению персоналом Евгений Викторович Макаров посетили промежуточный склад механического цеха, который, в свою очередь, является эталонным участком по внедрению системы KANBAN.
В настоящее время наметилась четкая тенденция к росту затрат на хранение запасов, что и стало причиной разработки систем «мгновенного» управления запасами, к которым относится рассматриваемая система KANBAN, разработанная корпорацией Toyota Motors, — одна из первых попыток практического внедрения системы «точно в срок».
Консультант по бережливому производству Алексей Болотов, прибывший из города Набережные Челны для налаживания этой системы на предприятии, представил Юрию Петровичу схематичный план движения деталей в ПРОСКе.
«Сущность системы КANBAN состоит в том, что все производственные подразделения предприятия снабжаются материальными ресурсами только в том количестве и к тому сроку, которые необходимы для выполнения заказа. Заказ на готовую продукцию подается на последнюю стадию производственного процесса (это цех окончательной сборки), где производится расчет требуемого объема незавершенного производства, которое должно поступить с предпоследней стадии. Аналогично с предпоследней стадии идет запрос на предыдущий этап производства на определенное количество деталей. То есть размеры производства на данном участке определяются потребностями следующего производственного участка.
Цель этой системы — исключить дефицит, чтобы уменьшить время простоев сборочного производства и всего предприятия в целом, а это 100% выполнение госзаказа».
Далее он объяснил, каким образом карточка КANBAN будет проходить рабочий цикл на складе, что исключает затаривание ненужными деталями в данный момент.
У Юрия Петровича сразу же возник вопрос и беспокойство по поводу персонала: «Понимает ли коллектив свои задачи, и есть ли необходимость в его обучении? Внедрение LЕАN-технологий, в первую очередь, необходимо донести до понимания рабочего. Необходимо менять психологический подход и ментальность людей. Один из недостатков на предприятии — это сдельная оплата труда, которая и стимулирует большие потоки не нужных в данный момент деталей. Это вопрос комплексный: должен, в первую очередь, работать экономический блок, и, во-вторых, необходимо пересмотреть систему мотивации, иначе мы не добьёмся максимальной эффективности. Нужно понимать процесс и его нормирование, только тогда на выходе мы получим своевременное, необходимое количество деталей. Надо учитывать, насколько эффективно работают технологии. Для того чтобы создать обоснованные нормы, необходима тесная взаимосвязь технолога с рабочим».
Основные преимущества системы KANBAN: короткий производственный цикл; высокая оборачиваемость активов, в том числе запасов; отсутствие или чрезвычайно низкие издержки хранения производственных запасов; высокое качество продукции на всех стадиях производственного процесса.
Анализ мирового опыта применения системы KANBAN показал, что данная система дает возможность уменьшить производственные запасы на 50%, товарные запасы на 80% при значительном ускорении оборачиваемости оборотных средств и повышении качества готовой продукции.
В общем и целом предложенный план понравился и был одобрен управляющим директором. Ведущий инженер по логистике производственно-диспетчерского отдела Сергей Голубник рассказал, каких результатов достигли благодаря системе 5С в ПРОСКе механического цеха: «В помещении навели порядок, убрали лишнее. Рассортировали и упорядочили размещение деталей на стеллажах. Неиспользованные стеллажи разобрали и сделали из них приспособления в виде кронштейнов для хранения рам. Обеспечили эргономичную удобную сортировку, комплектацию и выдачу деталей. Расконсервировали окно приема и обозначили время приёма и выдачи деталей. Этим самым сократили простои комплектовщиц, увеличили их работоспособность, что позволило своевременно скомплектовать заказы на другие цеха. В перспективе планируется провести капитальный ремонт и реконструкцию помещения».
Начальник ПДБ механического цеха Александр Ошлаков продемонстрировал Юрию Петровичу и Евгению Викторовичу электронную систему сменных заданий для рабочих и учет деталей на складе. Также он сообщил, что запускается Устав проекта «Создание производства системы «Прогресс». В нем указаны все цели и задачи, которые необходимы для снижения производственного цикла и увеличения скорости сборки машины, а также для снижения незавершенного производства. Результатом будет своевременное выполнение Государственного оборонного заказа и снижение добавленной стоимости на одного человека.
Алексей Болотов, в свою очередь, заверил руководителей предприятия, что первые результаты на сборке продукции будут видны уже в мае, если система будет принята и освоена одновременно на нескольких производственных участках.