>Будни внедрения производственной системы «Прогресс»
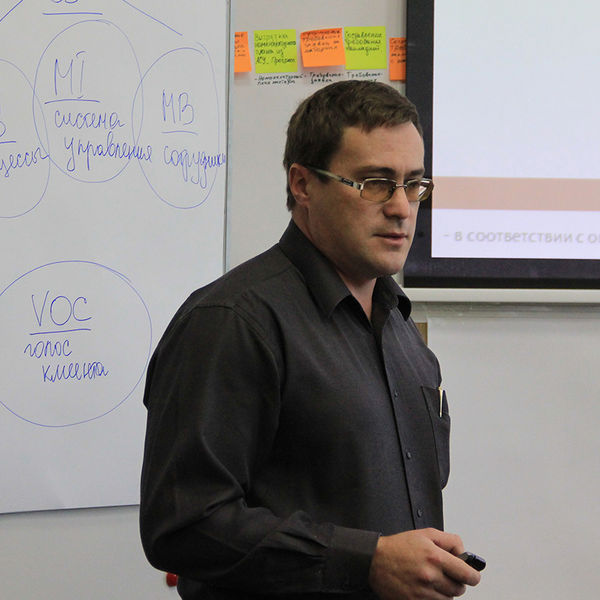
Бережливое производство (Lean-технологии) — это методология повышения эффективности организации, которая уже с успехом применяется на практике различными предприятиями России. При этом бережливое производство не столько фокусируется на совершенствовании процесса производства, сколько помогает современной организации совершенствовать свою деятельность на самых разных уровнях и делает ее по-настоящему эффективной.
О том, как бережливое производство работает на нашем предприятии и почему именно эта концепция управления способна придать новый импульс развитию авиационной компании «Прогресс», рассказали специалисты отдела бережливого производства.
Молодой коллектив отдела начал работу буквально с нуля. Не сталкиваясь прежде с бережливым производством на практике, молодые специалисты под руководством Тараса Владимировича Безручко, начальника отдела бережливого производства, начали работу над освоением данной методологии.
«Весомую поддержку в нашем обучении мы получили на форуме по обмену опытом с сотрудниками Lean-отделов других предприятий холдинга. Работа нашего отдела охватывает широкий спектр областей деятельности, поэтому мы как специалисты должны быть разносторонне подготовленными. С целью повышения квалификации сотрудников Учебный центр предприятия систематически проводит обучающие курсы по различным направлениям: например, летом этого года у нас была возможность пройти курсы по нормированию и 3-D моделированию в Unigraphics NX», — рассказывает инженер по организации управления производством 1 категории Александр Малашенко.
После поездки на форум началась крупномасштабная работа. В июне 2015 года был открыт проект «Внедрение системы общего производительного обслуживания оборудования (TPM)» на участке 8 механического цеха, руководителем которого является Александр. Основные цели проекта — внедрение системы TPM на эталонном участке механического цеха, сокращение случайных поломок оборудования в 10-15 раз и снижение числа брака продукции в 5-8 раз. В июне была собрана рабочая группа из 6 человек, в состав которой вошли заместитель главного механика А.Л. Корчевский, инженер по ремонту оборудования А.А. Кривоносов, производственный мастер механического цеха В.А. Кошель, слесарь В.П. Тарещук и токари Т.П. Луцак и Е.А. Баева.
Под руководством Александра Малашенко рабочая группа определила список оборудования, с которым необходимо работать в первую очередь. Первым итогом работы стало определение перечня основных дефектов в работе оборудования участка 8 механического цеха за 2014 год. В настоящее время руководитель проекта и члены рабочей группы с целью устранения выявленных дефектов составляют карточки визуализации обслуживания оборудования для каждого типа станка из определенного ранее списка.
«Карточки делаются для того, чтобы каждый работник мог наглядно видеть, что и каким образом ему необходимо делать для поддержания оборудования в надлежащем состоянии. Для каждой единицы оборудования в карточке схематично указывается описание зоны обслуживания, метод и инструменты для обслуживания», — рассказывает Александр. — Таким образом обслуживание оборудования становится понятным процессом, и его может осуществлять не только наладчик или механик-ремонтник, но и сам оператор, работающий за данным станком».
Кроме работы над проектом внедрения TPM Александр участвует и в других мероприятиях по рационализации производства: «В начале сентября отдел по бережливому производству выступил с предложением по цеху окончательной сборки — использовать альтернативные методы закрепления жгутов на стендах в целях сокращения материалоемкости путем уменьшения технологических припусков жгутов и кабелей с использованием драгметаллов для уменьшения расхода материала. Сейчас предложение по конструкции держателей и возможность применения приспособления в технологическом процессе рассматриваются главным технологом».
В августе отделом бережливого производства проводился аудит работы летно-испытательной станции с целью выявления проблемных мест. Созданная рабочая группа, в которую вошли сотрудники отдела бережливого производства Александр Пелипань, Александр Малашенко и Александр Левчук, провела хронометражные работы процесса движения изделия по технологическому циклу, начиная от передачи машины из цеха окончательной сборки и испытаний до завершения испытания. После чего к аудиту подключились сотрудники отдела организации труда, которые на основе проведенных хронометражных работ занялись нормированием техпроцесса.
«На основе собранных результатов сформирована карта потока создания ценности на летно-испытательной станции и подготовлен отчет, который поможет определить узкие места потока и способы их устранения», — объяснил Александр Пелипань.
С приходом в отдел нового сотрудника — руководителя проекта Михаила Юрьевича Милостного — продолжилась работа по реализации проекта повышения эффективности с использованием Lean-технологий на участке алюминиевого и магниевого литья литейного цеха.
«В кабинетах инженерно-технических работников были оформлены эталонные рабочие места и созданы схемы уборки кабинетов. В рамках работы по проекту был произведен расчет баланса мощностей по детали «корпус редуктора» за май-август. Кроме того, отдел бережливого производства разработал предложения для включения в программу обеспечения качества выпускаемой продукции на 2016 год, а в настоящее время всячески содействует продвижению Производственной системы «Прогресс» (ПСП) для последующего согласования с директорами по направлениям», — рассказал Михаил.
Параллельно с тем, что каждый из сотрудников ведет работу над своими проектами, в настоящее время отдел бережливого производства активно принимает участие в реализации проекта внедрения системы 5С на производстве.
По словам инженера по организации управления производством Александра Левчук, система 5С является одним из важных инструментов методологии бережливого производства. В настоящее время реализация проекта по внедрению системы 5С при активном содействии сотрудников отдела 508 на предприятии набирает обороты, а полученные результаты проведенной работы свидетельствуют об успехе предпринятых усилий.
«В настоящее время реализуется первый этап системы 5С — сортировка. Но уже сейчас мы можем видеть первые результаты — отношение людей к работе кардинально меняется», — рассказывает Александр. — «Повышается общий уровень культуры производства. Когда через определенное время повторно заходишь в цех, результат очевиден: везде чистота и порядок, все на своих местах, ничто не отвлекает от рабочего процесса».
«Как и в работе над любым другим проектом, здесь возникают определенные трудности. Основная трудность — это, конечно, первоначальная реакция людей. Многие из них сначала не понимают, зачем им что-то менять на своем рабочем месте. Но потом постепенно втягиваются и начинают осознавать. Естественно, на налаживание сотрудничества требуется время, и во многом это зависит от руководителей цехов или отделов, в которых мы работаем. Наша задача — не просто показать, как должно быть. За отведенный на каждое подразделение промежуток времени мы оцениваем его состояние, составляем план мероприятий и действуем по нему, помогая работникам подразделения «от и до» наладить свое рабочее пространство», — объяснил Александр Пелипань.
Кроме ведения проектов отдел по бережливому производству в лице начальника Тараса Владимировича Безручко, имеющего большой опыт преподавательской работы, проводит образовательные мероприятия для работающих и вновь принятых сотрудников предприятия.
«На базе Учебного центра два раза в неделю проходят инструктажи для вновь принятых сотрудников, а также еженедельно проводятся лекции по основам бережливого производства для переквалификантов — инженерно-технических работников и начальников цехов. С начала текущего года данные образовательные мероприятия охватили около 1000 сотрудников нашего предприятия. Все мероприятия и проекты, реализуемые отделом бережливого производства, имеют своей основной целью становление Производственной системы «Прогресс», — отметил Тарас Владимирович.
При организации производства невнимание именно к мелким проблемам и потерям может стать причиной неудачи любых мероприятий по повышению эффективности. Незначительные на первый взгляд потери имеют свойство накапливаться и в дальнейшем перерастать в существенные трудности. В таком случае важен уровень производственной культуры каждого работника и правильное его отношение к организации рабочего процесса, позволяющее не отвлекаться от решения более глобальных вопросов. Внедрение инструментов бережливого производства является наиболее оптимальным решением данной проблемы, что подтверждает практика каждодневной работы специалистов отдела бережливого производства.
Данные технологии направлены на поиск и устранение как мелких недочётов, так и более существенных проблем в производственном процессе предприятия. При соответствующей организации деятельности Lean— технологии становятся мощным инструментом, который можно направить на модернизацию любых процессов организации, что позволит ей успешно функционировать в жёстких конкурентных условиях современной рыночной экономики. Однако для более продуктивной работы технологий бережливого производства необходимо построение системы управления, контроля и постоянного совершенствования процессов организации, которой, в случае ПАО ААК «Прогресс», может стать Производственная система «Прогресс». Она позволит обеспечить ту самую необходимую для функционирования системы бережливого производства роль лидера, без которой внедрение Lean-технологий может продолжаться годами без видимого эффекта.