>Роботизированный комплекс для авиастроителей завода «Прогресс» представлен накануне Дня машиностроителя
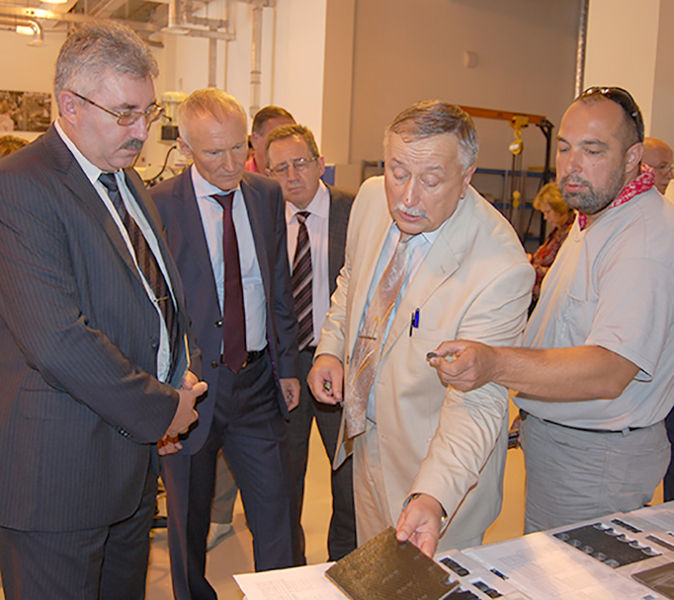
Накануне Дня машиностроителя в Приморье произошло знаковое событие, которое привлекло внимание специалистов в области развития робототехники и внедрения новых разработок в производственный процесс.
Интеллектуальный роботизированный комплекс для обработки деталей новых вертолетов, созданный в Инженерной школе Дальневосточного федерального университета, практически готов к установке на заводе «Прогресс». Такую оценку проделанной работе дал управляющий директор Арсеньевской авиационной компании, председатель Приморского регионального отделения Союза машиностроителей России Юрий Денисенко по итогам презентации установки, которая состоялась в ДВФУ. На завершающем этапе проекта ученые совместно со специалистами предприятия проведут отладку комплекса и настроят его на различные режимы. Ожидается, что до конца 2015 года комплекс будет перевезён и запущен непосредственно на заводе.
Молодые инженеры, занимающиеся этим проектом, рассказали корреспонденту газеты «ПП» о том, как они пошагово шли к конечной цели, созданию опытного образца. Они участвуют в проекте по созданию автоматизированного интеллекта робототехнического комплекса. Сейчас занимаются подготовкой управляющих программ для комплекса. На стенде представлены результаты экспериментов, которые были выполнены в рамках комплекса по определению методов обработки композитных материалов. Выполнены тестовые панели с разным сочетанием материалов. Использовались полимерные материалы: композитные (стеклоткань) и армированные стекловолокном, с углетканью и с наклеенной алюминиевой и титановой фольгой — в разном сочетании и разной толщины. Проверены эти панели на разных видах обработки, как механической — фрезерной, так и гидрообразивной, и лазерной. Панели — это элементы деталей обшивки вертолёта, и из-за разного назначения они отличаются по прочности и по своим свойствам. Были представлены 24 тестовых образца, чтобы учесть всю номенклатуру типов обшивки, используемых на предприятии заказчика. Из-за сложности представленных деталей только гидрообразивная обработка позволила решить и обеспечить всю номенклатуру тестовых панелей. И она была выбрана в качестве основной для роботизированного комплекса.
Спроектированный и собранный учеными ДВФУ комплекс способен обрабатывать гидроабразивным способом более 250 видов деталей размером до шести метров из 23 типов композитных материалов. Кроме того, робот обладает достаточным уровнем искусственного интеллекта, благодаря чему может самостоятельно распознавать линии, по которым необходимо вырезать детали. Заведующий кафедрой технологий промышленного производства Инженерной школы ДВФУ Константин Змеу во время презентации акцентировал внимание на уникальных возможностях комплекса, перспективах его усовершенствования и расширения спектра выполняемых работ.
Заведующий кафедрой технологий промышленного производства ДВФУ Константин Змеу:
— Сегодня происходит нечто среднее между предварительными этапами приёмки и шоу. Приглашены представители прессы, завода-заказчика, исполнительной власти, субподрядчики. Это плод многолетнего развития кафедры технологий промышленного производства (раньше она называлась «Станки и инструменты»). То, что в 90-х годах нам читали в университете как факультативный курс по робототехнике, и подразумевалось, что этого никогда не будет, в итоге сегодня всё это возвращается на новом круге и имеет прямое отношение к металлообработке, к технологии, выходит на прямую дорогу к использованию в производстве. Тогда роботы были неуклюжие, технология — сырая. Сегодня манипуляционный робот имеет много координат, это стандартная единица оборудования, которая дорабатывается для какой-то задачи, требующей пространственной гибкости. Его надо расположить вокруг какой-то детали. Здесь детали представлены в виде обшивки вертолёта. На производстве то, что делает робот, делает человек с помощью ножниц и лобзика. Если нужно сделать подряд 100 деталей, то робот не сделает ошибки, а человек, скорее всего, сделает. Здесь прорабатывается технология, как изготовить деталь сразу с множеством точных отверстий.
Есть выход также на технологии сборки отвёрточной. Сейчас вертолёт делают на стапеле, и это, фактически, индивидуальная сборка. Такая машина в перспективе может позволить делать сборку, и стапель будет не нужен. Вот у нас образец — две соединённые полусферы с множеством отверстий. Это мы испытываем резку объёмных деталей. Робот позволяет делать точные геометрические фигуры гораздо лучше, чем человек. Здесь, например, ни одной прямой линии нет, и человек в таком случае обязательно допустит ошибку, сделает неверно. Поэтому, конечно, более перспективно и производительно использовать в дальнейшем для решения производственных задач роботов. «Прогресс» участвует в разработке и софинансирует эту государственную программу.
Руководству авиационной компании продемонстрировали технологию резки реальной заводской детали. Через сопло под очень высоким давлением в 4000 атмосфер подается вода, в которую подмешивается специальный абразивный материал. Этот высокоэнергетический поток, летящий с троекратной скоростью звука, с высокой точностью разрезает деталь по заданной траектории. По словам разработчиков, такой способ позволяет максимально качественно резать самые разные композитные материалы, не нагревая их.
— На роботе получаются детали очень высокого качества, которые полностью отвечают всем требованиям для новых вертолетов: резы ровные, точные и не требуют дополнительной шлифовки, — оценил работу установки управляющий директор Арсеньевской авиационной компании «Прогресс» Юрий Денисенко. — С точки зрения производства в ДВФУ получилось создать уникальный комплекс. Мы очень ждем его, ведь использование установки значительно увеличит скорость и качество работы.
Интеллектуальный роботизированный комплекс для обработки полимерных композиционных деталей новых гражданских вертолетов Ка-62 создается в Дальневосточном федеральном университете в рамках гранта, выигранного по постановлению Правительства РФ № 218 «О мерах государственной поддержки развития кооперации российских вузов и организаций, реализующих комплексные проекты по созданию высокотехнологичного производства». Общий объем финансирования трехлетнего проекта составляет 405 миллионов рублей.