>Робот — на помощь авиастроителям
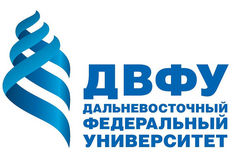
После того как в 2013 году ДВФУ выиграл грант в рамках постановления правительства РФ № 218 «О мерах государственной поддержки развития кооперации российских вузов и организаций, реализующих комплексные проекты по созданию высокотехнологичного производства», первое, что необходимо было решить — определиться с технологией. Поскольку в конструкции гражданских вертолетов Ка-62 используется более 20 видов сложных полимеров, крайне сложных в обработке, уже тогда это была не самая простая задача. Поэтому первые работы были связаны с тестовой резкой тремя способами.
Фрезерную механическую обработку исключили почти сразу. Тонкостенные детали оказались слишком податливыми. Лазерный раскрой показал сравнительно лучшие результаты. В отдельных случаях подобранный для многослойных композитов луч высокой мощности легко прорезал внутренние полимерные слои детали, но приводил к обгоранию наружных металлических покрытий. Решение о конструировании комплекса на основе технологии гидроабразивной резки, при которой в качестве режущего инструмента используется струя воды или смеси воды и абразивного материала (в нашем случае — песка), было принято не сразу. Как отмечает заведующий кафедрой технологий промышленного производства (ТПП) Инженерной школы ДВФУ, входящей в состав Приморского РО СМР, Константин Змеу, сложности есть и у этой технологии. Это засорение сопла трубы, из которого вылетает поток воды, особые требования к абразивному материалу и производственному помещению. Сюда же можно отнести требования по безопасности и экологичности производства. Однако именно этот способ показал лучшие результаты по наибольшему числу требований выбора технологии: точности, универсальности, качеству, прочности, экологичности, безопасности и другим.
Гидроабразивная резка
Вода камень точит, а что будет, если она будет не литься, а разгонять песок в трубке с давлением в 4000 атмосфер? В природе такая величина недостижима. Например, давление на дне Марианской впадины в четыре раза меньше. Скорость вылета пескоструйной жидкости при этом составит около трех махов, то есть где-то три скорости звука. Именно такой напор кинетической энергии и прорезал, наконец, все 22 полимерных композита, оставаясь при этом строго в контролируемых пределах.
Из-за сложности аэродинамического профиля обшивки вертолета от классической трехкоординатной схемы станка пришлось отказаться. Инженеры ДВФУ используют робот-манипулятор, рука которого имеет не три, а пять степеней свободы и радиус рабочей зоны почти два метра. Отметим, что для загрузки производственного комплекса на заводе давно запланирован выпуск широкого перечня деталей обшивки вертолета, поэтому их размер на выходе также сильно разнится. К примеру, наибольший диаметр детали — 6 x 3 х 1,5 метра, а наименьшей — 1 х 1 х 0,6 м. В компоновку комплекса также входит семиметровая высокоточная линейная направляющая. Робот перемещается вдоль направляющей, чтобы охватить все рабочее пространство над самой большой заготовкой.
На презентации, которая состоялась в ДВФУ и в которой, как мы рассказывали, приняли участие руководители Приморского регионального отделения Союза машиностроителей России во главе с управляющим директором ПАО АКК «Прогресс» Юрием Денисенко, комплекс продемонстрировал пространственный рез по контуру на заготовке со сложным геометрическим профилем, выклеенной из стеклопластика — одного из самых простых для обработки полимерных композитов. Изготовленная деталь уже сейчас готова к размещению в области хвоста вертолета. Этот результат по достоинству оценили члены московской комиссии и руководство завода «Прогресс».
Как уточняет младший научный сотрудник кафедры технологий промышленного производства Инженерной школы ДВФУ Максим Невмержицкий, работающий в рамках этого проекта инженером-конструктором, финальная компоновка комплекса в цехе завода займет примерно вдвое большее пространство, чем представленный в ДВФУ образец.
— Для этой презентации мы настроили «мягкий» режим резки: сниженное давление воды и небольшой расход песка, — объясняет Максим Невмержицкий. — Но рабочие режимы комплекса на производстве будут достигать предельных значений своих характеристик.
По стандартам безопасности промышленного производства мы спроектировали специальную кабину, которая закроет собой зону обработки, а также отделит рабочее место программиста-оператора. После монтажа в производственном цехе комплекс закроет собой кабина. Здесь, в рабочей зоне, будут смонтированы защитные барьеры, системы аспирации и водоотведения и прочие конструкции, необходимые для герметизации процесса обработки деталей. Кабина способна переместиться в сторону по собственным направляющим, тогда рабочая зона будет открыта для загрузки заготовок. Самые габаритные загружает кран. Установка заготовки производится на технологическом столе. Индивидуальный профиль каждой заготовки повторяет технологическая оснастка, которая жестко фиксирует деталь над столом, не позволяя ей ни деформироваться, ни смещаться в процессе взаимодействия с высокоэнергетичным потоком воды.
Перед обработкой кабина закрывается, робот распознает фактическое положение заготовки и начинает ее раскрой на основании спроектированной 3D-модели будущей детали. В процессе резания оператор находится в своей отдельной зоне и может следить за процессом через окно либо дистанционно на мониторе при помощи видеокамер. Контур раскроя наносится заранее. В рабочем инструменте робота установлена система технического зрения, представленная лазерными сканерами. По их данным система управления контролирует как сам рез, так и положение режущего инструмента относительно поверхности заготовки. В случае отклонений, вызванных, скажем, вибрациями, искривлением заготовки, ее отличием от 3D-модели, система управления сама скорректирует положение робота.
К слову, наш абразивный материал — это специально просеянный и подготовленный гранатовый песок, который встречается только в нескольких местах на Земле. Нам его доставили с пляжей Австралии, именно он подходит по всем характеристикам. Вода для резки используется обычная, водопроводная. Однако прежде чем попасть в сопло режущего инструмента, она проходит две степени очистки на станции водоподготовки, которая также входит в наш комплекс. В процессе реза песок, вода и частицы композита попадают в поддон, а оттуда по полотну конвейера автоматически поступают в шламосборник и канализацию. Наш робот также способен омывать себя и зону резания после завершения обработки деталей — мы спроектировали систему с замкнутым технологическим циклом, — уточняет Максим Невмержицкий.
Что нам стоит вертолёт построить?
Общее финансирование трехлетнего проекта составило 405 млн рублей: 220 млн направил «Прогресс», 185 млн субсидировало государство. Финальная приемка в полной комплектации, монтаж в цехе и работы начнутся в декабре, сейчас ожидается поставка последних комплектующих и проходит отладка системы управления, вносятся последние корректировки в режимы резания.
Инженеры-разработчики получили не только уникальный опыт, но и весомые научные результаты. В ходе создания комплекса коллектив кафедры ТПП ИШ ДВФУ подал ряд заявок на патентование найденных решений по способам резки композитных материалов и новые варианты конструкций технологической оснастки. Отметим также, что комплекс, совмещающий в себе технологию гидроабразивной резки, пятикоординатную обработку и полностью автоматизированный производственный цикл, в России был разработан впервые.
Как отмечает Константин Змеу, проект позволил поднять квалификацию сотрудников, что особенно ценно для молодых кадров. Обучение в Москве было необходимо для работы на современном оборудовании лидера отрасли производства промышленных роботов — немецкой фирмы «Kuka» и ведущего производителя промышленной автоматики «Siemens». В декабре при этом совместная работа с «Прогрессом» не заканчивается.
— С самого начала перед нами стояла очень напряженная по срокам задача. Конечно же, внедрение новой техники потребует авторского сопровождения. К такой работе на площадке завода мы готовы, — подчеркивает Константин Змеу. — При этом есть большая вероятность, что мы поучаствуем и в следующем конкурсе. Это дальнейшая автоматизация производства, связанная уже с литейными технологиями. Хочу отметить, что без бюджетного софинансирования любому предприятию сложно пойти на такие расходы. Я рад, что у «Прогресса» такая возможность есть.